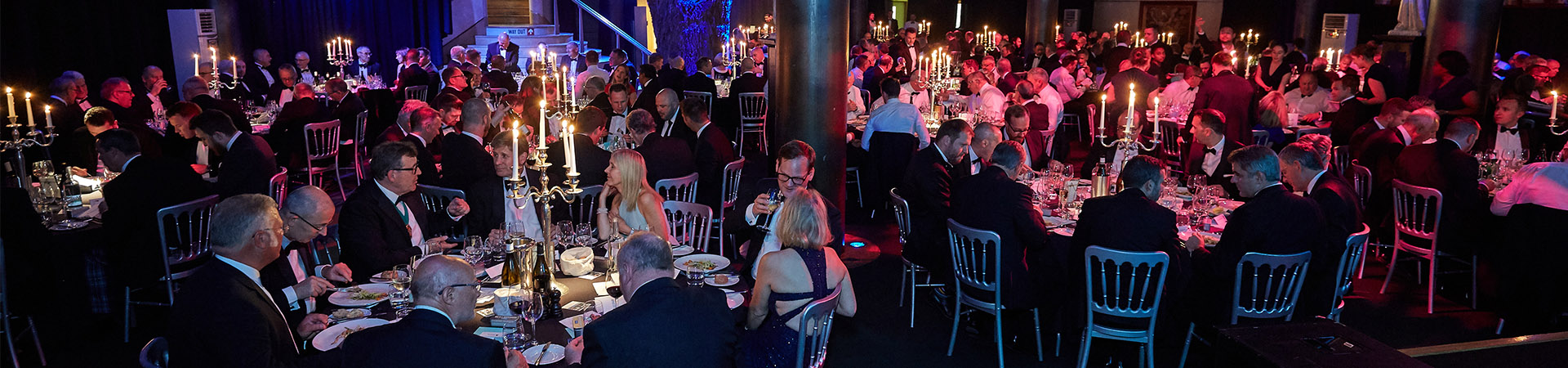
BCSA News and Insights
President's Column April 2024
15/04/2024
Category: President's Column
Until the construction industry develops zero-carbon materials, we all must applaud and recognise the current recommendations to “use less stuff” when designing our steel buildings.
Part of this current strategy is to design our buildings more efficiently by reducing the weight of the steel frame, which then requires less raw material and therefore results in lower greenhouse gas emissions at source. This approach satisfies Modules A1 and A2 in our carbon-footprint calculation tools, but often increases the manufacturing complexity due to the need for enhanced strengthening of the connection parts of the lighter steel components.
One other way to use “less stuff” is to design and specify more efficiently designed fabricated sections in place of standard rolled sections. However, this approach appears to have taken a backward step with the misconception that every current UK project can be delivered with steel sourced from Electric Arc Furnaces. In truth, the availability simply isn’t there yet. But by adopting either approach are we paying enough attention to the other potential consequences on a lighter frame design, and are carbon reduction and cost inseparably linked?
Increased fabrication complexity usually involves the need for additional materials, such as stiffeners or strengthening plates. And while this may still result in a lighter overall frame weight, these fittings are generally ignored in the overall project calculations, and are almost certainly ignored when evaluating the project cost and programme.
Lighter steel members are more difficult to handle in the shop, which can result in the fabrication and use of temporary lifting aids such as spreader beams or strong-backs. And since these components are part of the manufacturing process, the impact of the raw materials to produce these temporary members is not included in the overall project carbon calculation and so we are in danger of misrepresenting the actual values.
Lighter steel members also require additional passive fire protection to meet the project safety standards but again, since the design and specification of the fire protection is usually the responsibility of the steelwork contractor, the full environmental impact is often not considered during the primary steel design phase.
The same logic that applies to the handling, lifting and turning of the individual steel members in the fabrication shop is repeated on site, with the need to procure and fabricate additional steel components to use as lifting frames or strong-backs. In addition, temporary props or restraints may be necessary to ensure stability and robustness during the construction period, and again, the impact of these additional components is generally ignored in the overall project carbon valuation.
Any argument for ignoring the inclusion of temporary site-works due to their availability for re-use on other projects can equally be countered by the need to provide safe and simple access to the temporary components. And the supply, installation and subsequently dismantling of the temporary works is usually one of the more costly features of any project.
Additionally, a lighter frame can result in more individual members due to shorter spans and the resulting additional columns. The more members there are, the bigger the impact on fabrication shop hours, transport, corrosion or fire protection, and construction duration. Which brings us back to our currently excluded components of time and cost.
None of us would be reckless enough to disregard the need to “use less stuff”, but we must ensure that all the relevant “stuff” is being appropriately considered during the design.
Gary Simmons, BCSA President
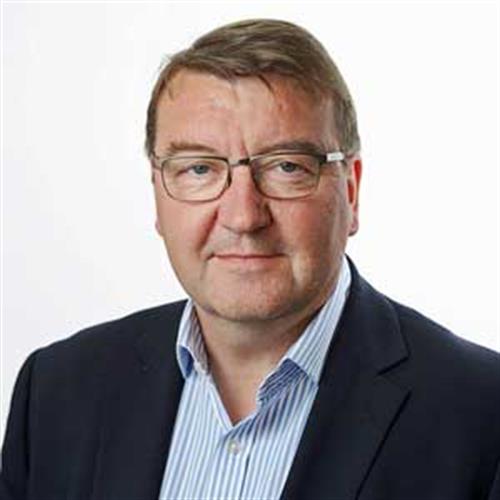
Previous article
06/04/2024
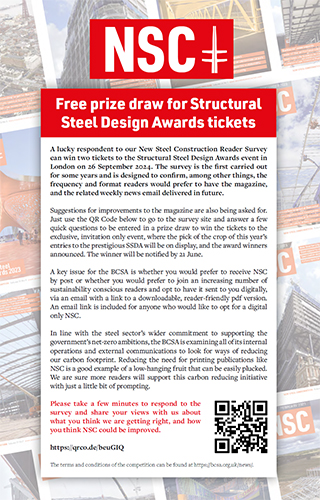
Complete the NSC Readership Survey to be in with a chance of winning 2 tickets to the SSDAs 2024
A lucky respondent to our New Steel Construction Reader Survey can win two tickets to the Structural Steel Design Awards event in London on 26 September 2024. The survey is the fi rst carried out for some years and is designed to confi rm, among other things, the frequency and format readers would prefer to have the magazine, and the related weekly news email delivered in future.
Next article
07/05/2024

A warm welcome to our new BCSA Stakeholder Member – Thames Welding Ltd
Thames Welding offers expert welding advice, training, certification and consultation to companies working with structural steel and aluminium.