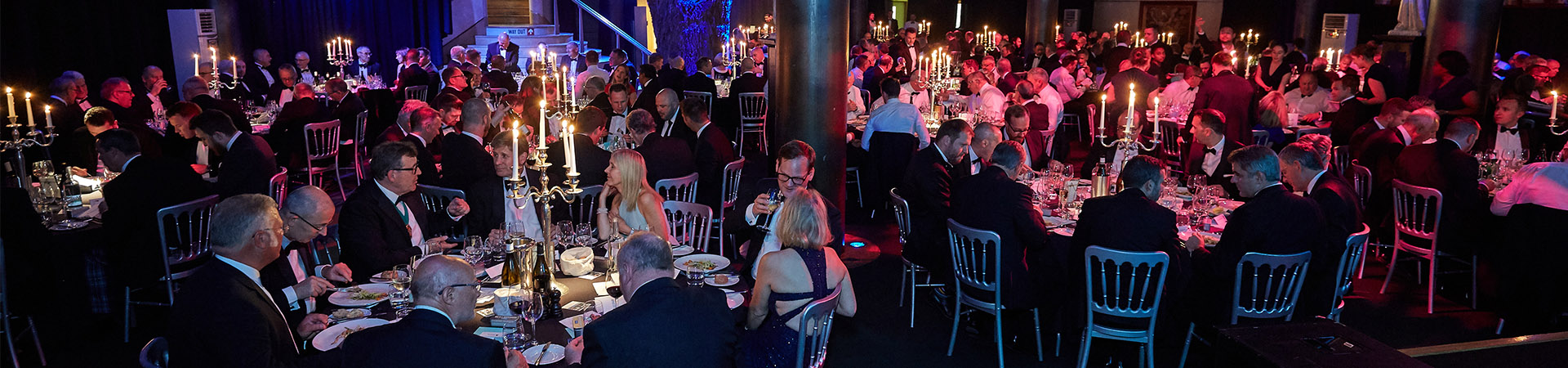
BCSA News and Insights
President's Column March 2018
27/03/2018
Category: President's Column
I'm hearing a lot in the press about new methods of construction, with terms like 'offsite construction' and 'design for manufacture' coming up more and more.
However, many people forget that steel framing is the original offsite framing material and is already delivering a huge range of advantages to clients.
Fabrication of individual steel pieces takes place offsite under controlled, highly regulated and safe factory conditions, where the use of digital design and leading-edge fabrication systems deliver precision-engineered components with minimum waste.
Steel components are further pre-assembled or fabricated into modules either offsite or at the site at a low level. Structures are often prototyped or trial built offsite to ensure a perfect fit when the fabricated steel modules undergo final assembly on-site.
Already many steel structures have the M&E incorporated offsite - some examples include motorway gantries with the lighting and digital signage already fitted, transfer bridges for large manufacturing plants, and even the risers in high-rise buildings. This means that the majority of the value add for structural steel occurs offsite - in some cases up to 90%.
The benefits delivered by an offsite steel programme are those that the government is now looking to extend through the rest of the construction sector.
A faster on-site construction programme means government construction targets can be met more easily, the programme will be less affected by adverse weather, and a shorter on-site programme is more cost-effective.
Fewer people are required on-site which helps to mitigate issues around skills shortages, and improves on-site safety. The need to work at height is reduced due to the majority of the work taking place offsite, also providing a skills and safety benefit.
Offsite steel manufacturing occurs in a controlled environment with factory production control and the adoption of automation ensuring consistency and reliable quality, and creating scalability.
Digital design for manufacture and assembly, including full Level 2 BIM, has created new skills in the sector. And the stable long-term nature of jobs in a steel fabrication factory assists in the training of a specialist workforce.
So what's next? The structural steelwork sector is not standing still and continues to invest in modern automated plant and equipment. With the sector having adopted Level 2 BIM and able to undertake digital design for manufacturing, it is now looking at implementing digitisation throughout the complete supply chain.
But for the sector to continue to move forward, clients and main contractors need to adopt new procurement models to drive earlier supply chain engagement. This will create further efficiencies for offsite manufacture, in particular opportunities for further offsite integration between sub-trades.
Tim Outteridge, BCSA President
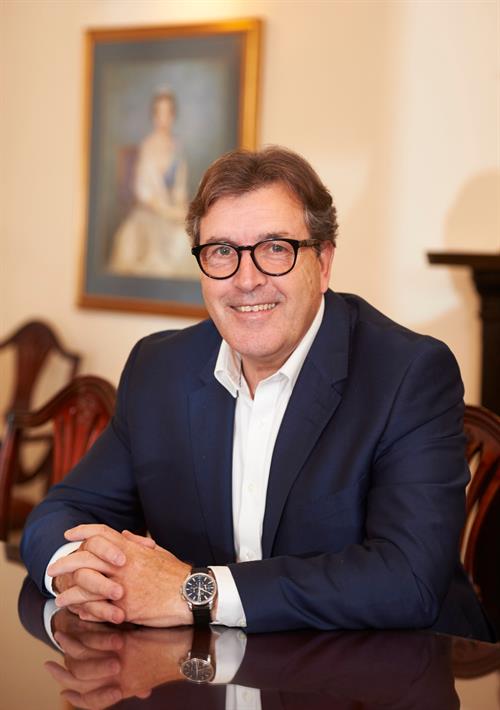
Previous article
01/03/2018
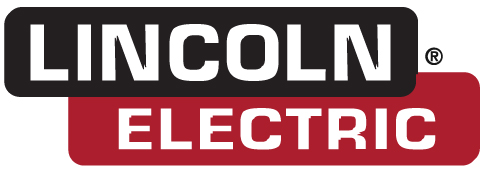
BCSA welcomes new member Lincoln Electric
BCSA is pleased to welcome Lincoln Electric (UK) Ltd into Industry Membership.
Next article
16/04/2018
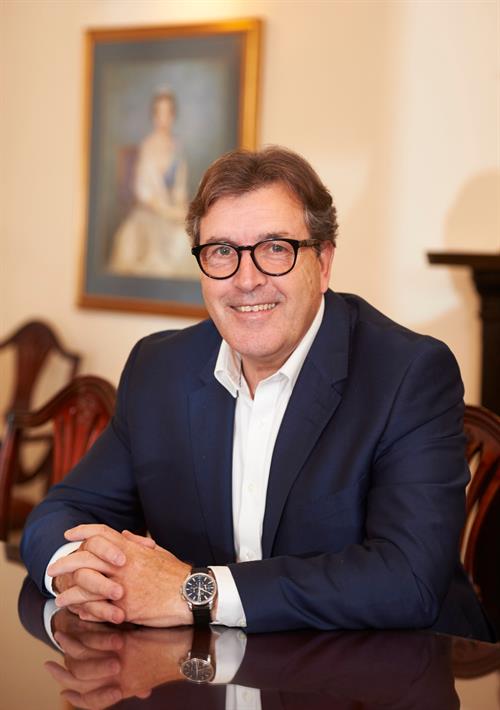
President's Column April 2018
The UK economy is bumping along, we have read about construction material costs rising across the board, tightening labour availability, and the latest Construction PMI shows subdued growth conditions.So, what does 2018 and beyond hold for the structural steelwork sector?Given these general conditions, the outlook is solid - as is the sector itself. In 2017 structural steelwork consumption in the sector was 894,000 tonnes. We did see an easing in consumption last year, but 2018, 2019 and...